
The Interfor sawmill at Adams Lake is one of the largest employers in the Shuswap, thus it has been on my wish list to visit and see firsthand this state-of-the-art industrial site that is the third largest in the province. It had been over 50 years since I last worked there and so much has changed, especially after the most recent rebuild in 2009 that cost $200 million.
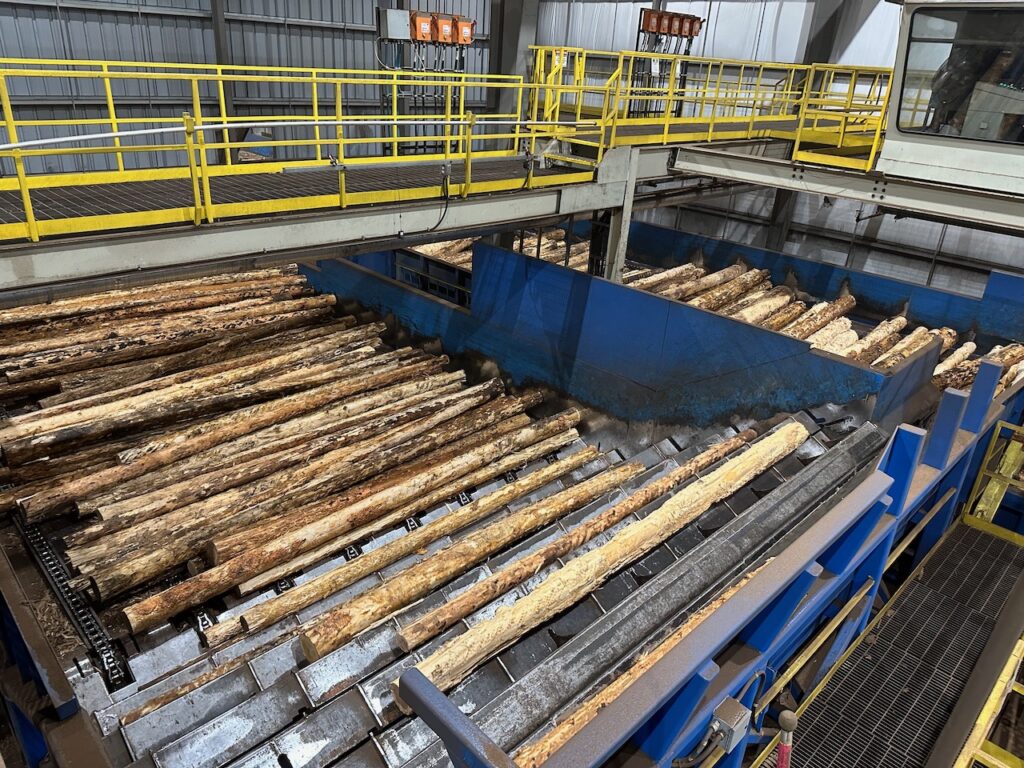
The mill has a voracious appetite for logs, and it churns out upwards of 100,000 board feet of lumber per hour, enough to build ten homes. The entire log is utilized, with the bark used as hog fuel, the chips turned into pulp at the Kruger Mill in Kamloops and the sawdust made into pellets in Lavington. Defective logs are also sent to Kamloops for pulp and the oversized logs that are greater than 25 inches in diameter go to smaller mills in Barriere, Westbank and Lavington.
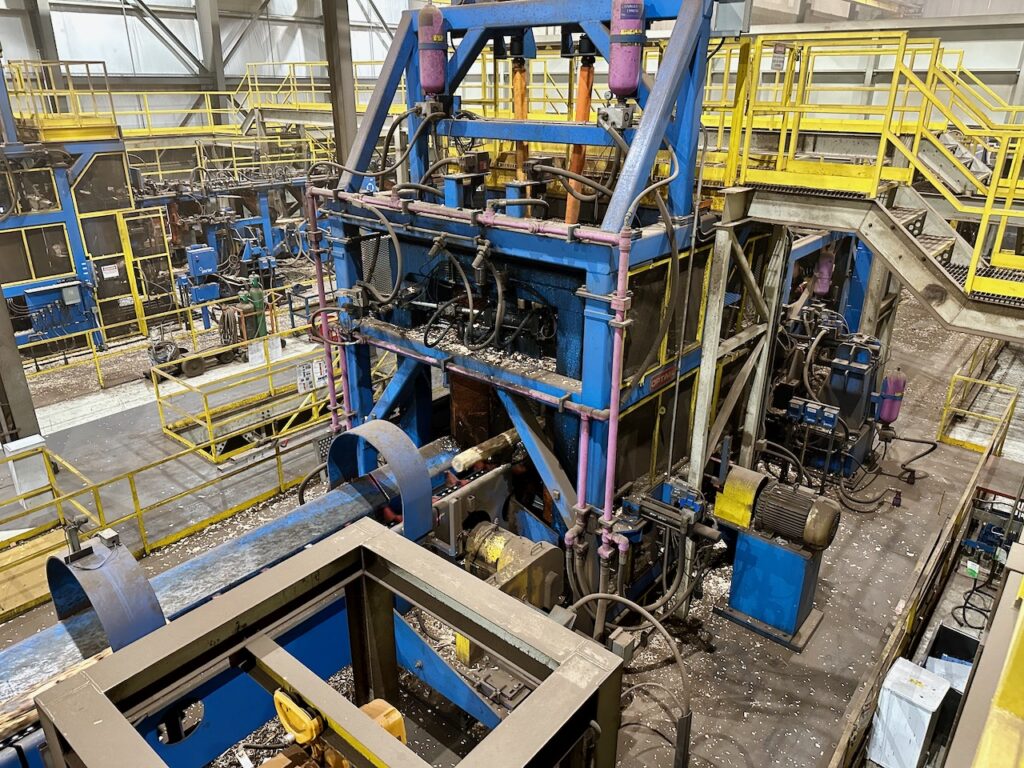
Mill manager Ryan Oliver was my tour guide as we went through the facility beginning with the two canter lines where the logs have two sides cut off with band saws that takes just two seconds per log. Each log is examined by computers with cameras that direct the machines to turn and position the logs to make the optimum cuts. At the next step the cants go through one of three gang saws that cut the logs into either one- or two-inch-thick boards or speciality sizes for export. As the newly cut boards move along, a single worker flips any board that either must be re-edged or made into chips if it is defective.
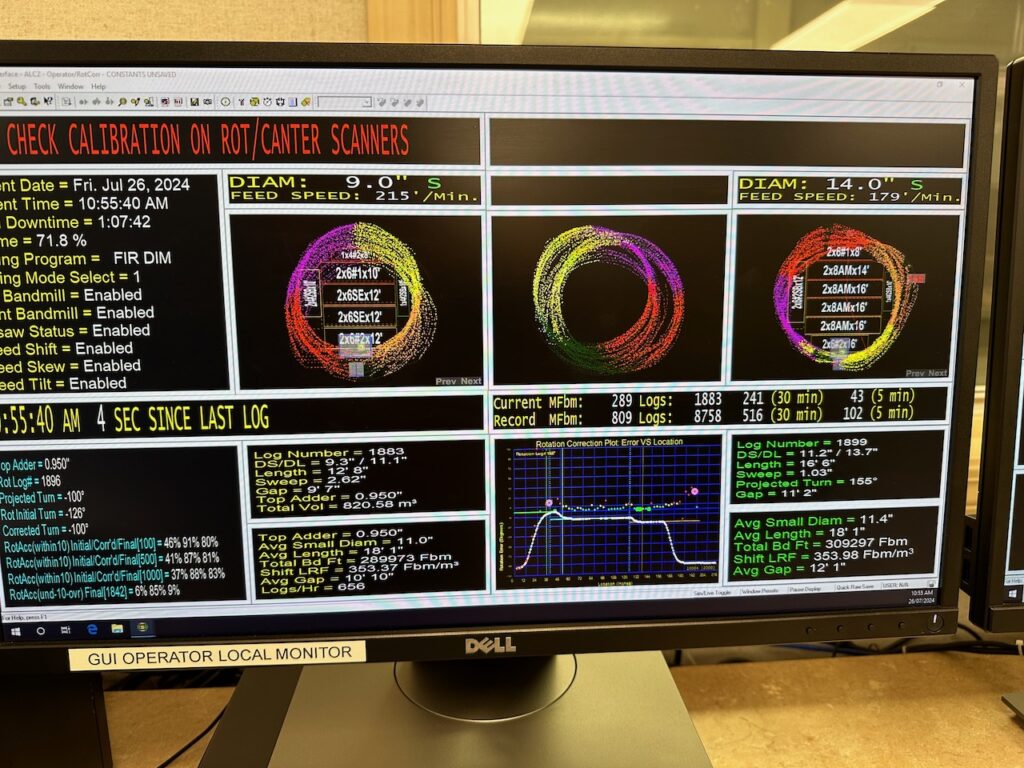
Computers track each board as it moves down the line according to its grade, quality and moisture content and each board is sent to the correct pile. Most of the workers are observing each computerized operation either at stations or on screens and are ready to make any adjustment needed or cut and remove any logs or boards that have gone astray. The next step is the kiln, where the boards are dried in 40 to 100 hours depending upon the moisture content as they are slowly moving through continuously.
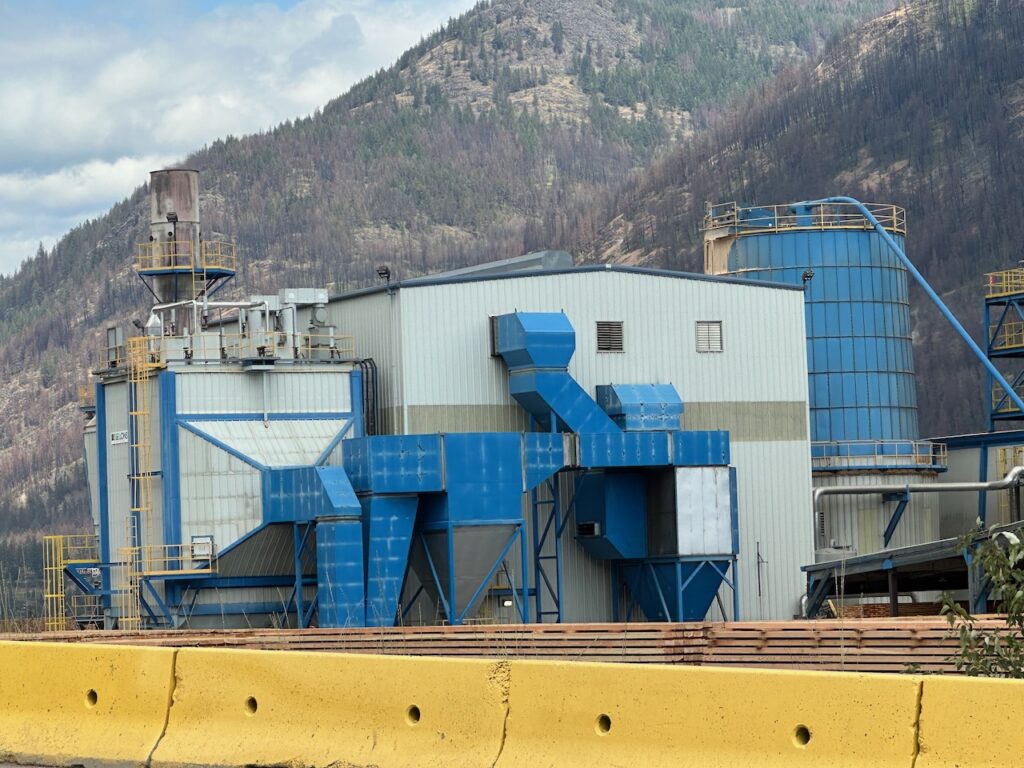
The kiln has also been modernized, with the heat produced by burning hog fuel, which is transferred to oil that is piped through the facility. All that is emitted from the burner is pure vapor, as the smoke is re-burnt. Long gone are the days of the beehive burners that filled valleys with hazardous smoke. Although the ash now goes to a landfill, there are trials underway to utilize it for fertilizer.
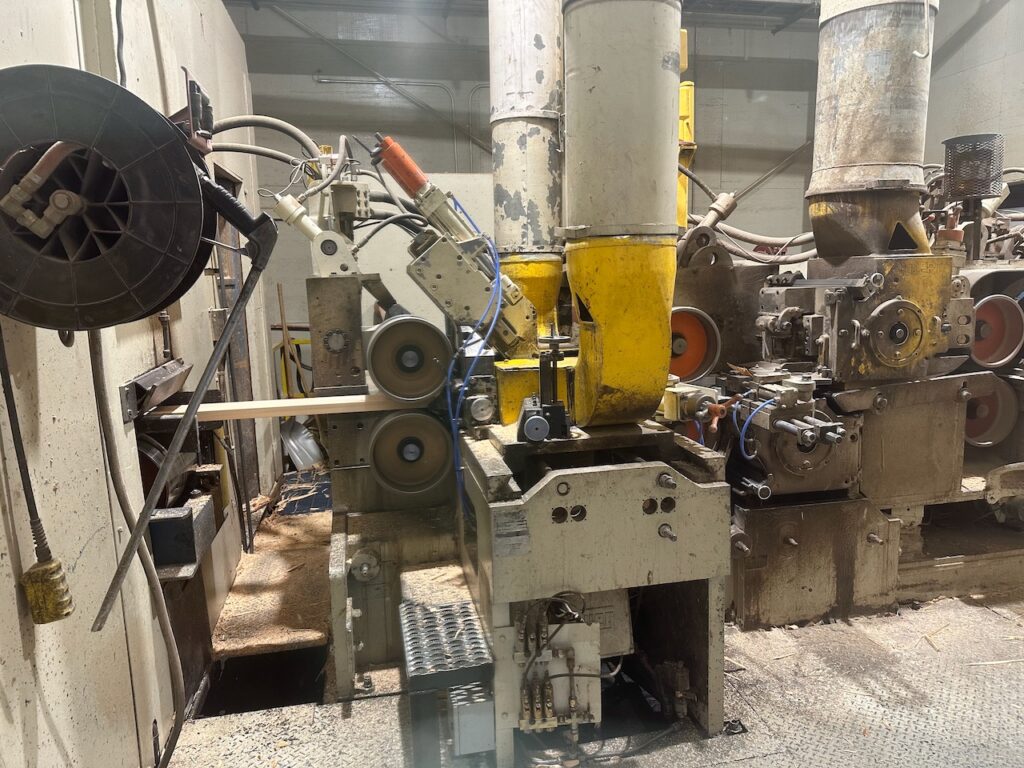
From the kiln, the rough boards move to a tilt hoist, which removes the strips. From here the boards go through the planer. Prior to the modernization, each planed board had to be graded by a worker who determined its quality and if it is needed to be trimmed. Now every board is tracked after it has been scanned using four types of technology: a geo-metric laser that determines the feel and shape, a vision camera that see knots and stains, a tracheid laser that tells the slope of the grain and the shape of the knots and an x-ray that determines the stiffness and machine stress rating. There are up to 2,000 different options for each board.
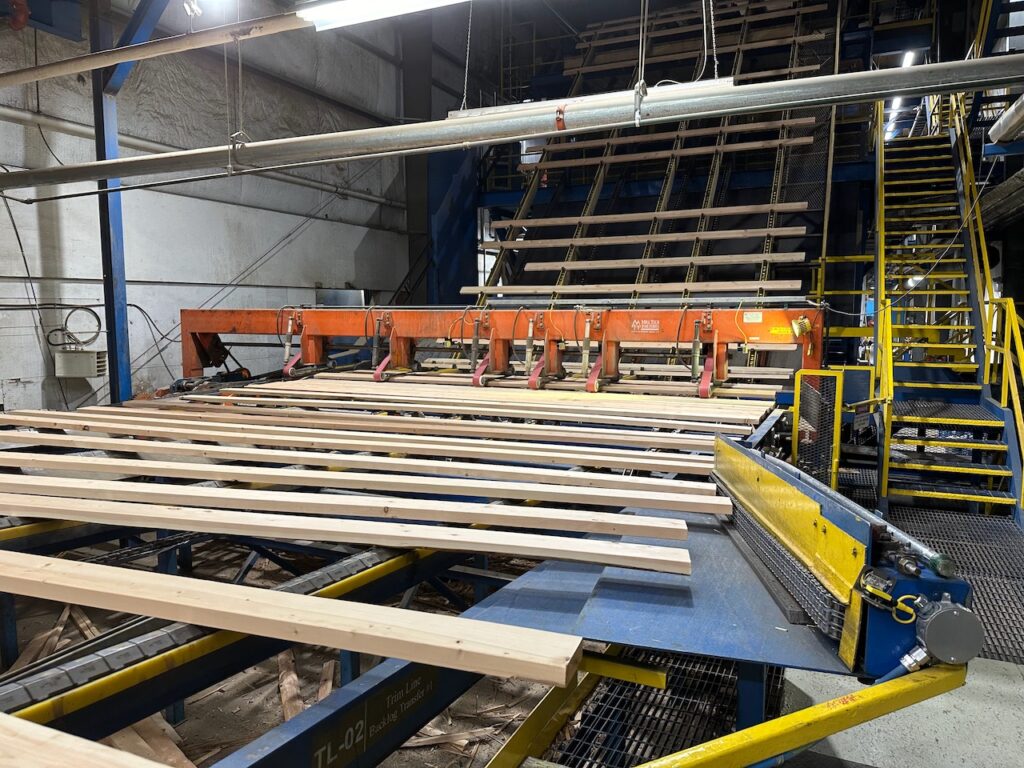
The final step for each piece of lumber is when it lands into one of 67 different piles according to its width, length, and grade. Boards with the highest MSR are used for speciality products such as trusses and laminated beams. Even the short pieces of lumber that were off are utilized by speciality companies that use them for small boxes and other products. The final step is when the boards are piled, painted with labels and wrapped for shipping.

The contribution that the sawmill makes to the local economy is significant. Although it is a non-union mill, the approximate 200 mill workers receive wages that are at par or better than union wages and they get profit sharing. Most of the high-tech computerized equipment used in the mill was manufactured in Salmon Arm by either USNR or Milltech. In addition to the mill workers, there are the hundreds of loggers, equipment operators, foresters, tree-planters, forest technicians who work to supply the mills with logs and make sure the cutblocks are replanted and become “free-to-go” forests.
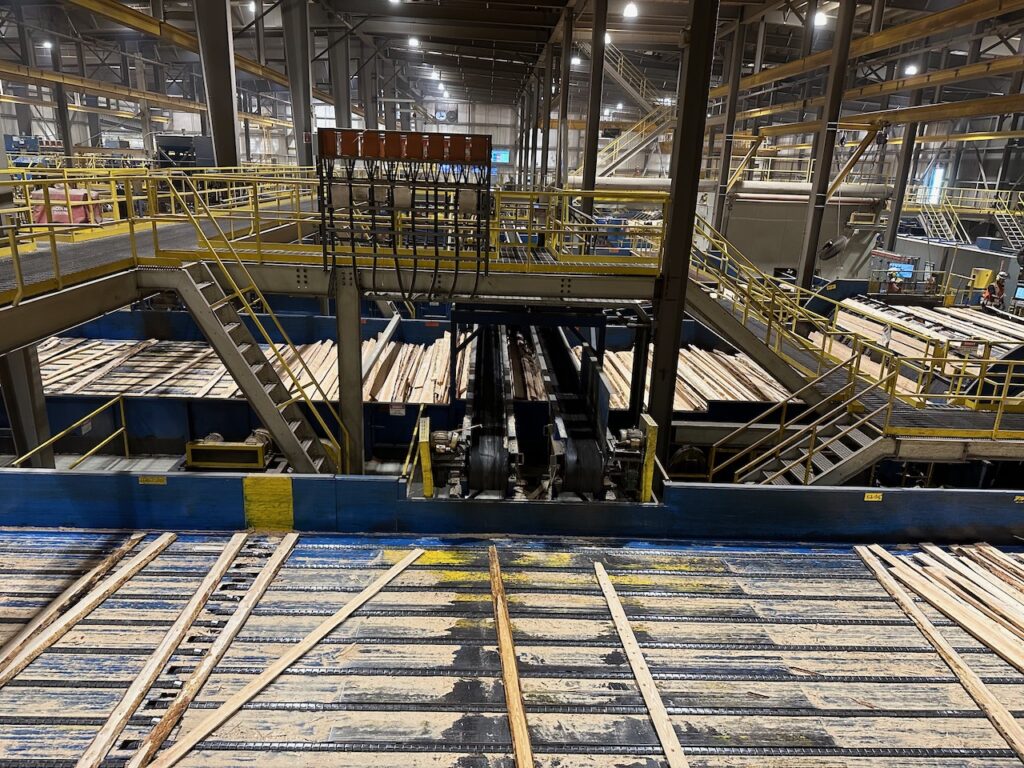
POSTSCRIPT
Most of the logs being sawn at the mill now come from salvage logging after last year’s massive wildfires burned up the forests adjacent to Adams Lake and in Squilax and the North Shuswap. These logs are drier and result in more dust in the mill. The logs that are not stored in the are watered prior to entering the mill to lessen the amount of dust.
It was not until the last few years that visitors were allowed to have tours through the mill. After the rebuild, Interfor made sure that only the employees were allowed in the mill, because they did not want the technology shared because it was so new and at that time, unique. However, as mill manager Ryan Oliver explained, there are now many mills in the province that utilize the same or similar technology. Thus, the mill is quite willing to show off this state-of-the art technology that is capable of churning out lumber at record speed.
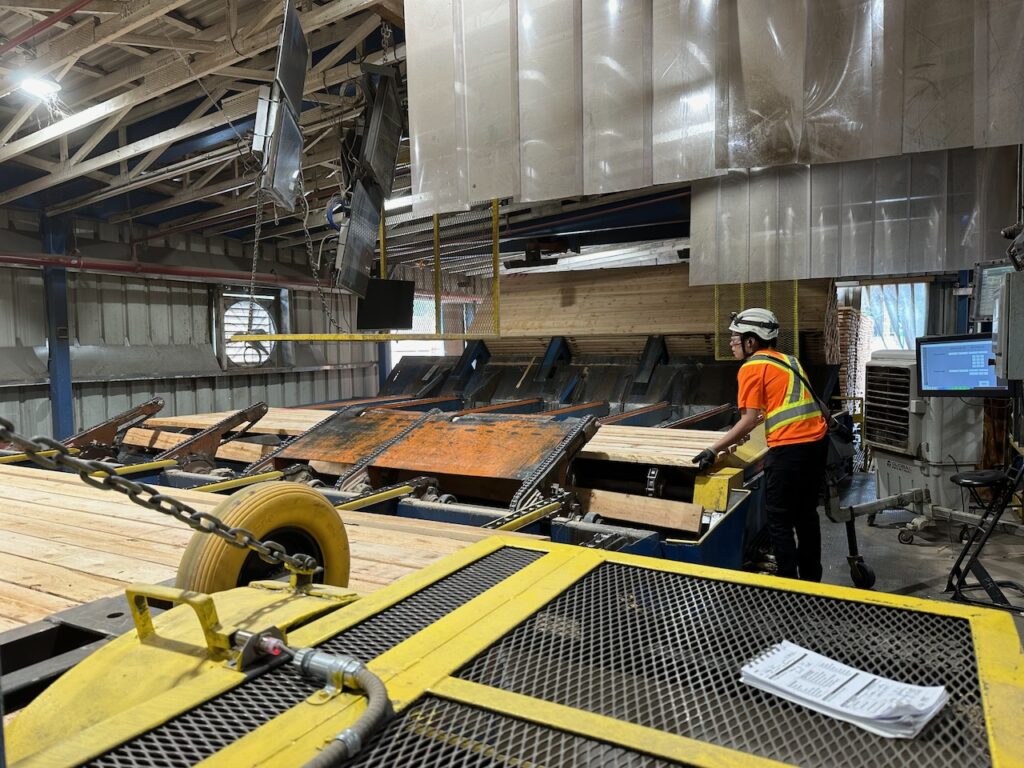
Here are photos of some of the signs that further explain the advanced technology used at the mill:
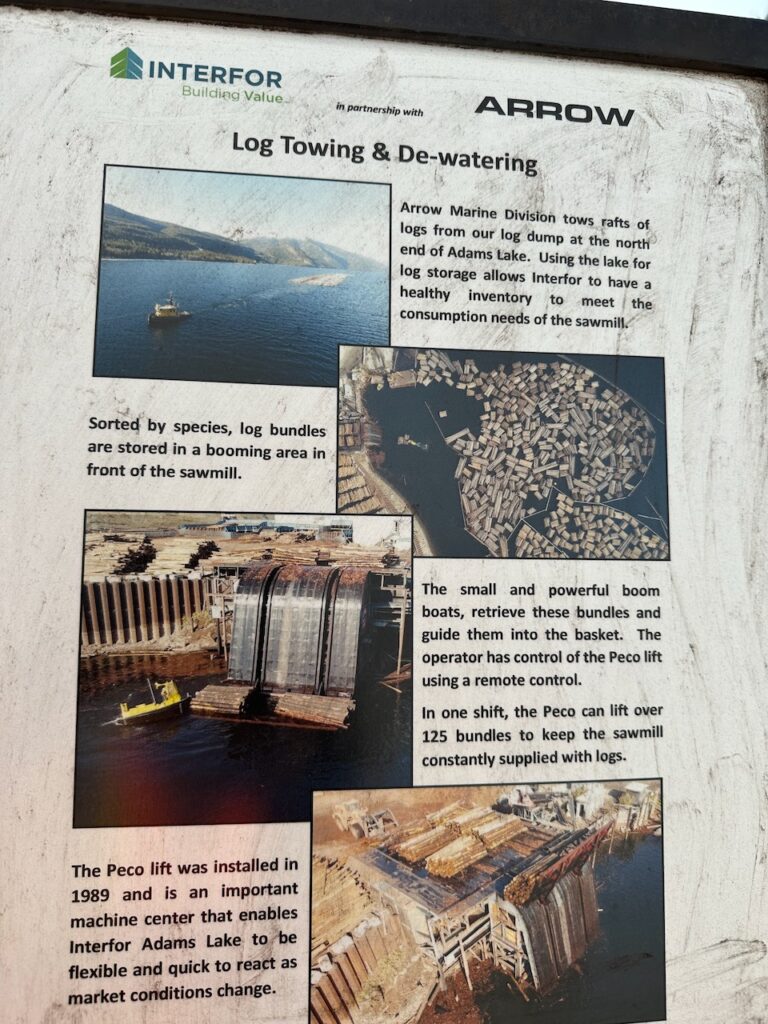
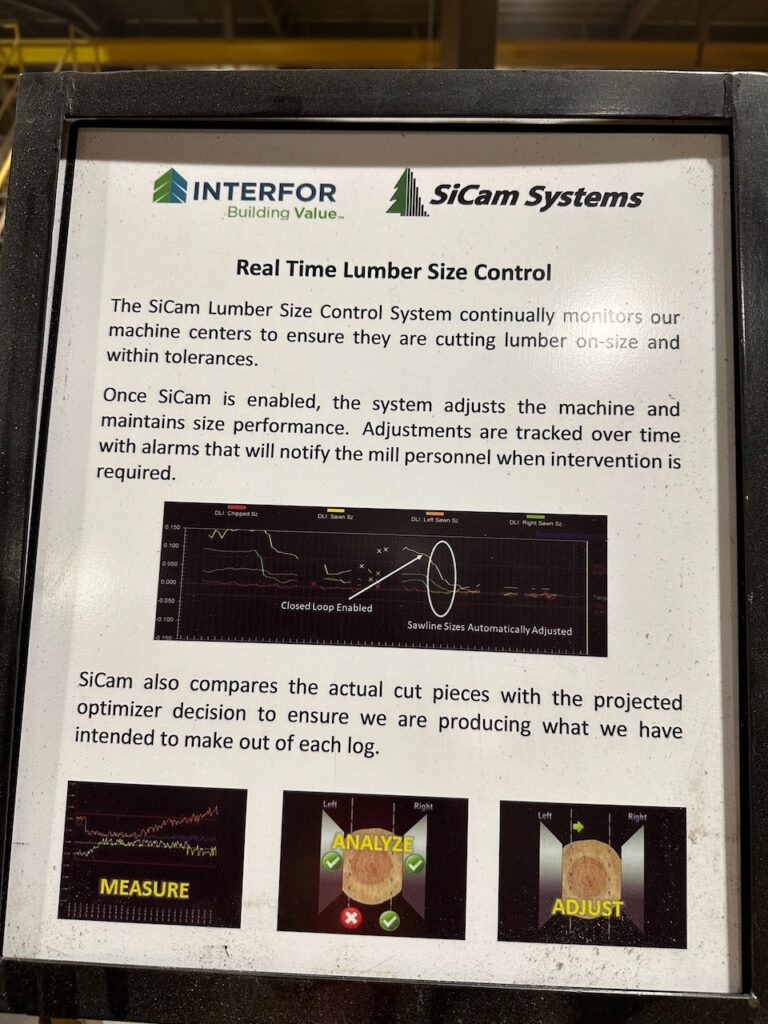
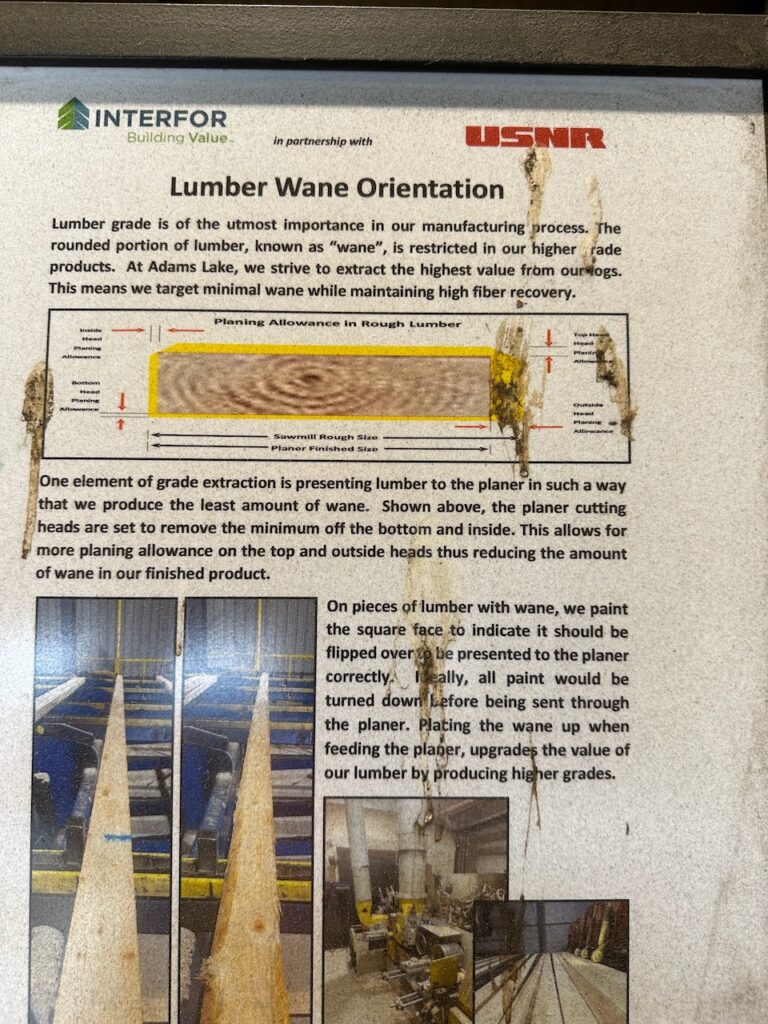
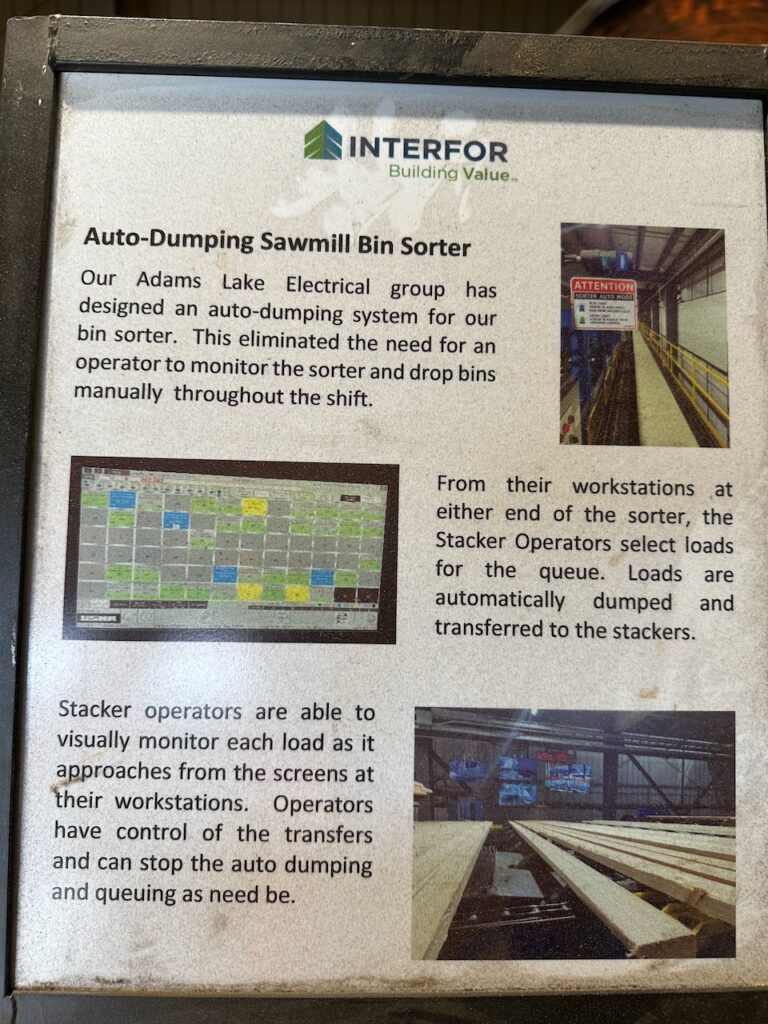
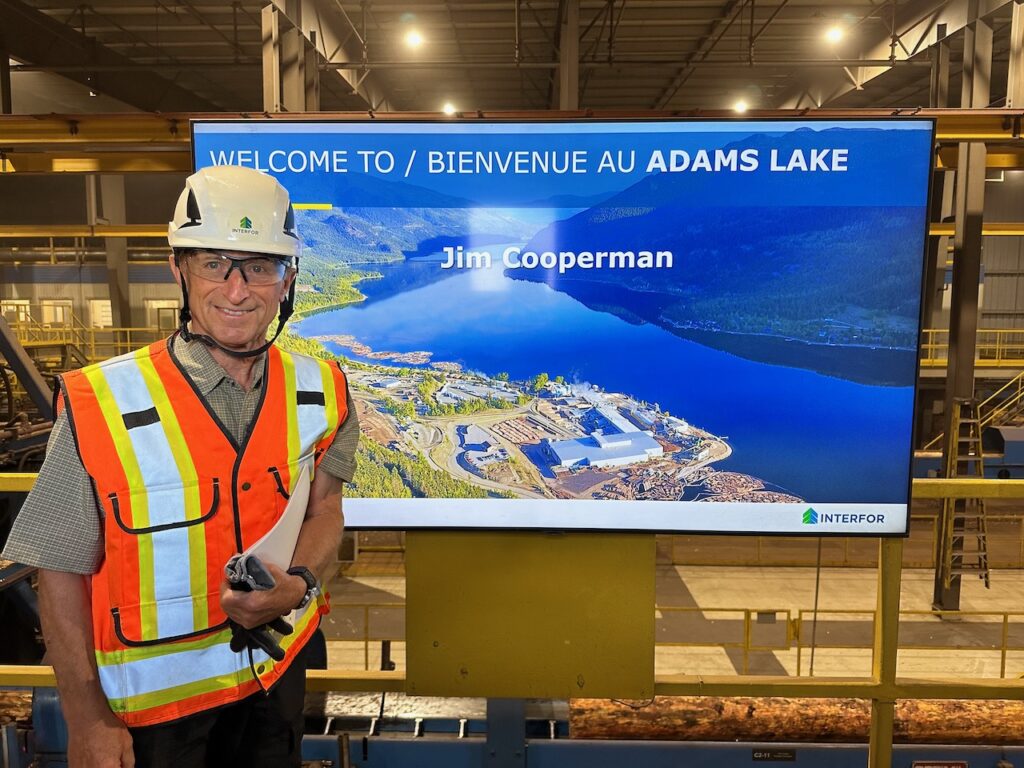